Joseph B. Howell, Ph.D., LLC is a clinical psychologist who practices in Anniston, Alabama. 6.18b). The technology is able to develop details finer than 200nm [50]. (B) Projection microstereolithography (PSL) printing of high-resolution shape memory Eiffel Tower and stent with tunable dimension parameters. The DLP bioprinter also can print an intricate structure with high resolution (~1m) and with fast printing speed (~30min, mm3/s) regardless of the layers area and pattern [18]. Once the print is complete, the print is filled with thermoset resin, which cures inside the mold, all within the 3D printer. professional and religious organizations have engaged Dr. Howell to present to them on these and 9.18D shows that a shape memory Kelvin foam lattice structure and a printed chess structure can self-heal after the cut. Measurements were done in compression mode at a frequency of 1Hz and with a heating rate of 5C/min in the temperature range of 30C200C. A promising application of DLP is the manufacturing of midsoles. During the manufacturing process, the print head ejects the droplets onto the print stage under the low temperature, layer by layer. Figure9.18. SLA 3D printers don't cure layers slowly, but DLP does it quicker with the single flash of the layer's image! This can result in lower costs and less waste. Moreover, this method results in a significant time advantage and allows structures to be fabricated in a matter of seconds to minutes. Use of HA filler resulted in polymer stiffness similar to PLA, providing scaffolds well suitable for bone tissue engineering. German manufacturer Nanoscribe has developed a process known as two-photon polymerization, wherein a laser directs two photons of near-infrared light at a photopolymer resin. Rapid. It's important to keep in mind the fact that DLP is unable to produce parts with great strength, it's much more suited for making accurate and beautiful parts which are not intended to deal with the load.These days, the most common applications of DLP include the dental, medical and jewelry industry. A prototype of the phone-based digital light processing 3D printer from Taiwan Tech. Developments have also been made around vat photopolymerization that has allowed for a form of DLP 3D printing to be performed with visible, white light. Interestingly enough, the tiny bit of space left between the vat's bottom and the build plate is specified by the layer height of the future part. Dentists work with tiny complex parts every day, making sure each patient is satisfied. By continuing you agree to the use of cookies. Ge etal. Chan et al. Hi there! In order to facilitate cell adhesion, the scaffolds were covalently modified by conjugation with fibronectin before seeding with the bone marrow progenitor cell line derived from mice. polySpectra makes functional materials for advanced additive manufacturing in Berkeley, California, USA. These parameters are highly dependent on the concentration and types of photopolymer and photo-initiator used for the resin. [165] utilized the graded stress by the nonuniform volume shrinkage during frontal photopolymerization to fold thin films into 3D origami structures. Naturally, everything starts with a 3D model. Because the resin is cured into layers with a digital image of the very layer, the image size dictates the resolution. As mentioned, the printing material should be biodegradable and biocompatible so that living cells can be directly involved inside the droplets during the printing process. 74.2D) [17]. It has to be mentioned that scaffolds produced from PEGDA are not biodegradable as such. The key is a specialty photopolymer resin that cures with visible light so that the smartphone can be used as the light projector. is also a regionally known expert on the Enneagram, a method Both are 3D printing processes that work with photopolymers, but DLP uses a more conventional light source, such as an arc lamp, rather than a UV light as in SLA. No matter how many LEGO bricks form a curved surface, it's not going to be 100% smooth, right? Schematic illustration of the preparation process of the tBA/HDDA crosslinked network made up of tBA monomers (soft segments) and HDDA crosslinkers (hard segments) via digital light processing (DLP). Resins are also more tricky to handle, but their shelf life is also limited. Some of the latest DLP machines get sub 50um accuracy. This doesn't mean that big parts printed with DLP have bad quality, not at all. Exposure of the parts to the UV light ensures the parts are cured correctly and ready to use. DLP uses a shallow vat of resin, and uses everything within the vat for each printing. The innovative midsole of the Adidas Futurecraft 4D sneaker seeks to provide extreme comfort and great performance for runners. Figure 8.36. (2009b) have utilized biodegradable PPF-based formulation to fabricate 3D scaffolds with a home-built DLP system. The mass and composition proportion of the five kinds of photosensitive resins. Fig. Great dimensional accuracy and the fast print speed make DLP a rather desirable choice when it comes to the manufacturing of parts. Felzmann et al. In a recent publication by Heller et al. Scheme diagram of deformation and recovery process in the fold-deploy tests of DLP-printed SMPs. Besides printing SMP, DLP also enables digital manufacturing multimaterial for desolvation-based shape shifting [70,71,112,130,133,163,164]. Well, for this exact reason we'll first explain what components make up a DLP 3D printer before describing how the printing process works. Traditionally DLP and therefore SLA usually weren't used for the manufacturing of parts which are under load, but more for the parts which prioritize the aesthetics and dimensional accuracy. Ali Davoudinejad, in Additive Manufacturing, 2021. Dr. Howell was a Fellow in clinical psychology, 9.18A shows the design and print part of a multimaterial SMP as an artificial arm with sequential recovery capability [134]. A schematic of a DLP 3D printer. Stereolithography (SLA), Digital-light-processing-based SLA (DLP-SLA), and inkjet-based methods are the most common 3D printing methods to manufacture cell-laden hydrogels. After the slicing is done, We are left with a PNG stack of images that is flipped through like a picture book, one layer at a time until you reach the last layer of the model, our default layer thickness is 100um. Because hearing aids need to be individually suited for each customer since everyone has a different ear shell, the process of making the hearing aids is exhausting and long-lasting.

This video explains the process and working of DLP printers in detail - by Professor Bill Hammack, Department of Chemical Engineering, University of Illinois. Based on your browser settings it looks like you may prefer to view this page in German, would you like to switch languages. (A)Reproduced with kind permission of AAAS from Reference X. Kuang, J. Wu, K. Chen, Z. Zhao, Z. Ding, F. Hu, D. Fang, H. J. Qi 2019.Grayscale digital light processing 3D printing for highly functionally graded materials Sci. The resolution of DLP-based printers is dependent upon the focal size of the reflected light beam and is usually on the order of a few microns. With DLP-based bioprinting, an entire plane of pattern is projected onto the prepolymer solution at a time, and the stage moves while the printing patterns continuously refresh. The build platform lowers into the resin to the point when only a tiny bit of space is left between the vat's bottom and the build plate. The main purpose of slicer software is to give the user the ability to set all the parameters for the printing job, and then prepare a file that can tell the printer what to print. In the preprocessing preparation, the CAD model is sliced into layers, and each layer is converted into array of droplets. Adidas is one of the brands which utilized a DLP 3D printer in the production of a sneaker named Futurecraft 4D. Michael Molitch-Hou, in Additive Manufacturing, 2018.

Adv., 5 eaav5790; (B) Reproduced with kind permission of Nature Publishing Group from Reference Q. Ge, A. H. Sakhaei, H. Lee, C. K. Dunn, N. X. Fang, M. L. Dunn 2016.Multimaterial 4D printing with tailorable shape memory polymers Sci. With the capability of modulating scaffold mechanical property, DLP-based bioprinting can also be used to print tissue models and disease models (Cha et al., 2014; Grogan et al., 2013; Ma et al., 2016; Soman, Tobe, et al., 2012; Zhu et al., 2017), including but not limited to vasculature network (Zhu et al., 2017), aligned muscle scaffolds (Liu et al., 2020; Ma et al., 2019), and liver microarchitecture (Ma et al., 2016).
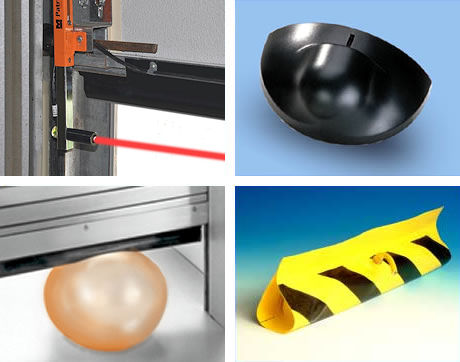
During the preprocessing preparation of SLA, the 3D CAD model is sliced into several layers based on the desired layer thickness. Schematic representation of the digital light processing vat polymerization process, in a bottom-up configuration. DLP-based bioprinters have several advantages over inkjet- and extrusion-based bioprinters, thus highlighting their versatility. The wavelength of the UV light is 405nm, and the power density is 12501450W/cm2, which are both intrinsic parameters of this printer and could not be adjusted. Naturally, DLP comes with its own pros and cons. Zhao etal. All vat polymerization technologies build parts curing the resin into a solid layer by layer with a certain light source, therefore creating a three-dimensional structure. Other firms have since released other versions of what is often called continuous DLP, including EnvisionTEC and 3D Systems. Origin has partnered with large chemical companies such as BASF, Henkel, and DSM to create unique photo polymers at a low cost that can be used to mass manufacture products. Leave a comment if you think new innovations need to be added to this article! Vat polymerization technologies, which include both SLA and DLP have revolutionized the way hearing aids are made with a goal to make them both cheaper and better-fitting. Direct Light Processing was originally developed in 1987. 4D printing by digital light processing printing. Fig. 9.19C shows that the polymer network with spatially variable degrees of monomer conversion and cross-linking density led to different monomer desolvation and swelling ratios in water. DLP-based bioprinting systems incorporate light sources, digital micromirror device (DMD) chips, motorized stages, a holder for bioinks, an optional motorized printing head, and a computer control system that coordinates all components (Figure 2.1C) (Gou et al., 2014; Hribar, Soman, Warner, Chung, & Chen, 2014). The objects, coated with iron oxide on their tips and platinum loaded onto their tails, could be guided magnetically, helped in their propulsion [51].
Although I'm still a student, I've developed my passion for business and 3D printing at an early stage of life. The SLA and DLP-SLA methods are used to form photo-crosslinked polymer networks when placed under a light source. Due to it curing the entire layer at once, its much faster than SLA. Carbon is a young company which invented 'Digital Light Synthesis,' a 3D printing technology similar to DLP, but improved.
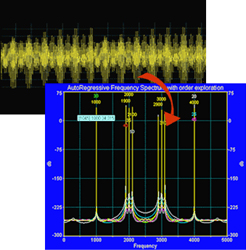
Using this method, a reversible shape-shifting structure with self-expanding/shrinking structures can be achieved (Fig. These very pixels which make the image of the layer used for curing the resin are later translated into three-dimensions. DLP using multivat or grayscale curing enables printing multimaterial with location-specific material properties for SMPs. The major difference of DLP from laser-based SLA is that DLP uses a projection of ultraviolet (UV) light (or visible light) from a digital projector to flash a single image of the layer across the entire resin at once. How is DLP cheaper than other methods of 3D printing? The layer thickness was set to be 50m and the exposure time for each layer was set as 30s. The thermal stability and crystallization behavior of the DLP-fabricated specimens were analyzed by a TG/DSC synchronous thermal analyzer (STA449F3, Netzsch, Germany). 5.7 shows the schematic of the DLP process. The dental industry is all about precision, right? On the other hand, the laser in the SLA printer has to go "point by point" to cure a single layer. What kinds of materials can be used in DLP printing?
hong kong light district The main components of a DLP 3D printer are the following: digital light projector screen, DMD, vat (resin tank), the build plate and the elevator for the build plate. That leads to expect you'll encounter the DLP printing technonology and DLP printed parts more and more, and that it will show up in many new applications. The construct can be printed by repeatedly depositing droplets with desired patterns in a layer-by-layer fashion. They were all obtained from Shan Dong Yinglang Chemical Co., Ltd and were utilized as received without any purification.
Fold-deploy tests were conducted in the following four steps (as shown in Fig. This all leads us to the first benefit of DLP when compared to SLA. To deposit the printing material onto the printing stage, the laser focuses on the desired point at the laser absorbing layer, then the focused region is heated and increases its volume to push a droplet of material onto the stage. Detailed ring printed on a DLP 3D printer. The chemical structure, photoreactivity, mechanical properties, and degradation behavior, as well as the cytotoxicity of the resulting materials were thoroughly evaluated. As for any 3D printer, the first step of the printing process is uploading a 3D model to the printer. For Wevolver readers they are providing a free specification sheet of their newest materials. DLP 3D printers are usually used for the making of models of patient's mouth. DLP (Digital Light Processing) is a 3D printing technology used to rapidly produce photopolymer parts. Photosensitive resins with five mass fractions of HDDA ranging from 10wt.% to 50wt.% were prepared. So many people are searching for ways to find happiness in this world of difficulties, relationship problems and emotional pain. Limitations of DLP printing include strong odors produced by melting photopolymers in the printing process, and the risk of warping in larger items. Using the same approach, Yang etal. The printing must be performed under sterile conditions when the cell-laden hydrogels are printed, and the printing materials should be mostly water-based and biocompatible. The testing procedures were performed in the following five steps: (1) Heating, where the samples were heated from 30C to 10C above Tg at a rate of 3C/min and then thermally insulated for 10min; (2) deformation, where the samples were exerted an external force at a rate of 0.1N/min up to an applied strain (load) around 10%; (3) cooling, where the external force remaining unchanged, the samples were cooled to 30C at the speed of 10C/min; (4) fixing, where the external force was removed; and (5) recovery, where the samples were reheated to 10C above Tg. The Rf can indicate the ability of the SMPs to fix the mechanical deformation applied in the programming of process, while the Rr demonstrates the ability of the material to recover to its original shape. In his ground-breaking book from Balboa Press entitled; Becoming Conscious: The Enneagram's Forgotten Passageway, Dr. Howell reveals simple, yet profound ways to know our deepest selves and the other people in our lives. 1.16). Follow us along to the following paragraphs where we'll explain how DLP works and point out the differences with SLA. Mater. Because the size of the object printed is dependent upon a projector and resolution of the image it projects, DLP printing is not suitable for very large items. Digital light processing (DLP) is another type of SLA. Figure5.7. Apart from learn more. The properties of the printing materials such as porosity, mechanical stiffness, and degradation are easily adjustable by controlling the light exposure times, the concentrations of the polymers, and the photoinitiators. The gradient in multimaterial desolvation and swelling can be utilized for shape shifting. Note that this is different from a technique like FDM: With 3D printing techniques that use machines with multiple motors on gantrys, like FDM printing, you need a different kind of file in a format called g-code. The preparation process of the other four ratios of photosensitive resins was identical with that of the resin containing 10wt.% HDDA. Not only is the process fast, but it also opens 3D printing up to the large range of existing resins used in the reaction injection molding process [48]. Having received his Table 8.3. Taken together, DLP-based bioprinters can be used to fabricate complex 3D structures with fine features in a matter of seconds. Dynamic mechanical analysis (DMA) was carried out with a Perkin Elmer Diamond DMA apparatus to evaluate the dynamic thermal-mechanical properties of the DLP-printed specimens. On the other hand, DLP-SLA method projects each cross-section image directly into the polymer solution to fabricate the tissue constructs at once instead of using a laser beam (Fig. polySpectra's technology enables them to deliver materials with a spectrum of tailored properties from a single chemical system.Author Leo Greguric mentioned in the article how recently there have been significant advancements in the materials and thus the quality and strength of produced parts.I spoke with polySpectra CEO Raymond Weitekamp, who explained that they've spent thousands of hours and hundreds of thousands of dollars characterizing the thermomechanical properties of dozens of additive manufacturing polymers. Inkjet-based 3D printers are designed based on the traditional 2D inkjet paper printer (Fig. The printing material is stored inside the chamber at the print head under low temperature to maintain low viscosity of the material, such as thermally sensitive gelatin- or collagen-based polymer solution. The DMD chip consists of millions of micromirrors that allow for precise light projection patterning by turning individual micromirror to the on or the off state independently throughout the printing process.
Sitemap 33