The fabricated prototypes of the functional parts and the valve are shown in Figure 4d,e. The flow rate of the valve can be estimated as: where P is the initial inlet pressure, P is the pressure gradient, R is the initial flow resistance of the valve, and R is the resistance increment. With more than one hundred years of designing and manufacturing experience behind us, The Specialty Mfg. ; resources, X.Z. To quantitatively study the effect of the inlet pressure on the flow rate, we divided the flow rate curve into three phases based on the flow performances induced by the inlet pressures. Pugliese M., Ferrara F., Bramanti A.P., Gigli G., Maiorano V. In-plane cost-effective magnetically actuated valve for microfluidic applications. and A.E.O. As for the deflection of the membrane, various mechanical [16,17], electrostatic [18,19], pneumatic [20,21], magnetic [22,23], piezoelectric [24], or thermal [25] mechanisms have been proposed. Xia Y., Whitesides G.M. The standard deviation of the flow rate under sinusoidal wave pressures was 0.31 mL/min, which was equivalent to a flow variation of 7.75%.
Inertial-ordering-assisted droplet microfluidics for high-throughput single-cell RNA-sequencing. Warkiani M.E., Tay A.K., Guan G., Han J. Membrane-less microfiltration using inertial microfluidics. The flow variation defined as the relative pulsation to the mean flow rate was calculated as a ratio of the bilateral tolerance of minimum to maximum flow to the overall mean flow rate.
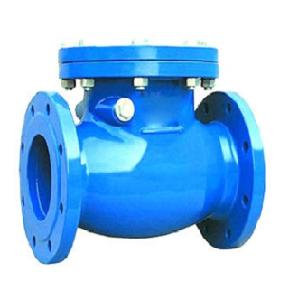
A low cost and quasi-commercial polymer film chip for high-throughput inertial cell isolation. (a) Simulated velocity magnitude in the valve. In comparison to the active valve, a passive valve doesnt require any external power, and it regulates the flow rate of liquid through autonomous adjustment of flow resistance. To solve this problem, we designed an ellipsoid surface in the control chamber and two micro-sized holes in the membrane to allow liquid passage into the control chamber. To this objective, we examined the prototype valve under time-dependent varied pressures. (a) Valve flow rate under static pressures. Takehara H., Jiang C., Uto K., Ebara M., Aoyagi T., Ichiki T. Novel microfluidic valve technology based on shape memory effect of poly(-caprolactone). The cover has the inlet while the bottom has the outlet, with diameters 800 m and 600 m, respectively. Thus, the valve could be used for high throughput sample processing in biological cell separation [36,37]. Moon H.S., Je K., Min J.W., Park D., Han K.Y., Shin S.H., Park W.Y., Yoo C.E., Kim S.H. Czilwik G., Messinger T., Strohmeier O., Wadle S., von Stetten F., Paust N., Roth G., Zengerle R., Saarinen P., Niittymaki J., et al. The When the inlet pressure was increased to a certain threshold value of Pt, the membrane deformed dramatically to approach the wall of the control chamber, inducing a highly increased flow resistance in the control chamber. Two through holes with a diameter of 1500 m were designed in the cover and the seal layer to form the liquid chamber (see the cross-sectional view of the valve). A review of microvalves.

Oh K.W., Ahn C.H. Fully integrated lab-on-a-disc for nucleic acid analysis of food-borne pathogens.

(951) 686.2852 Fax (951) 686.6328, Relief, Backpressure, Bypass & Anti-Siphon Valves, Aquariums and Marine Organism Conservation, Handling of Dry Chlorine and the Use of Plastic Valves, ROI: Advantages of Plast-O-Matic Products, Regional Managers & Factory Representatives, Authorized Distributors (password required).
National Library of Medicine Temperature: -30 C - 80 CPressure: 3 bar - 230 barFlow rate: 380, 14 l/min. The system without the valve driven by mouth blowing showed some dramatic flow fluctuations, with a mean flow rate of 10.44 2.05 mL/min (19.64% variation). Zhang X., Zhu Z., Ni Z., Xiang N., Yi H. Inexpensive, rapid fabrication of polymer-film microfluidic autoregulatory valve for disposable microfluidics. (c) Flow rate of the system operated by mouth blown air. Zhang C., Xing D., Li Y. Micropumps, microvalves, and micromixers within PCR microfluidic chips: Advances and trends. Fabrication of the microfluidic passive valve.
trunnion (f) Image showing the micro-holes in the membrane at position A in Figure 4d. ; project administration, X.Z.
forged valve steel check lift seal pressure name about navigating our updated article layout. We also demonstrated some smart function abilities of the valve in combination with a gas-driven flow system for obtaining high throughput and stable flow delivery under low driving pressures.
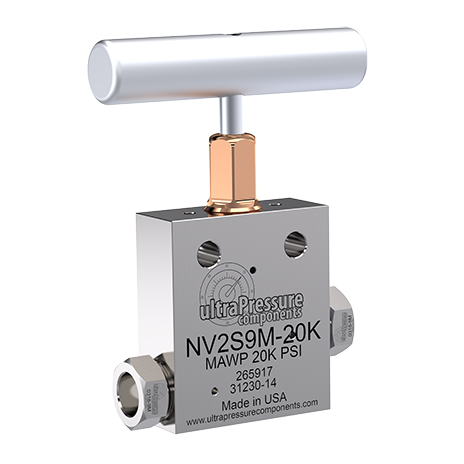
The new PMC design is here! As the inlet pressure was afterwards increased from 12 kPa to 17 kPa, the flow rate started to slowly increase, and the flow rate could not be maintained constant anymore in the test phase. In most of the traditional membrane valves, the fluidic channel is designed with a rectangular cross-section which characteristically leaves a dead zone at the corners upon the deflection of the membrane. We obtained a mean flow rate of 4.03 0.17 mL/min (flow variation ~4.22%) in the above pressure range. Chen C.-F., Liu J., Chang C.-C., DeVoe D.L. As the commercial syringe pumps or peristaltic pumps are bulky in size while expensive in cost, it is necessary to develop a cost-effective small sized pump. Kim T.H., Park J., Kim C.J., Cho Y.K. The control chamber has an ellipsoid surface, which connects to the valve outlet for liquid output. In the 6 kPa to 12 kPa pressure phase, we found that the flow rate was getting regulated, as it maintained a nearly constant value regardless of pressure change. (b) Flow rate of the system operated by an air blower. In the first phase, the flow rate was in direct proportionality to the inlet pressure, and it increased steadily as the pressure increased from 1 kPa to 6 kPa. Use the filter above to find your part number or call us at 973-256-3000, Plast-O-Matic Valves, Inc. The .gov means its official. High-pressure on-chip mechanical valves for thermoplastic microfluidic devices. Temperature: 0 F - 225 FPressure: 0.5 psi - 125 psi. http://creativecommons.org/licenses/by/4.0/. When inlet pressure is sensed the sealing disc is pushed off the valve seat opening the valve. Flow rates of the microfluidic passive valve under varied inlet pressures. For example, it can be applied to provide accurate sample fluids for high throughput cell sorting and concentration [40]. Schematic 3D architecture of the microfluidic passive valve. Zhang X., Xia K., Ji A. This paper proposes a novel microfluidic passive valve comprising of a liquid chamber, an elastic membrane, and an ellipsoidal control chamber, which actualizes a high flow rate control under an ultra-low threshold pressure. Zhang W., Lin S., Wang C., Hu J., Li C., Zhuang Z., Zhou Y., Mathies R.A., Yang C.J. and transmitted securely.

As the processing rate of cell separation and concentration can be several mL/min, a valve with the function of high throughput flow control will be very effective for the miniaturization of the microfluidic cell sorting system [36,37]. However, Series CKD requires a minimum back pressure of 1/2 PSI to close. A multi-layer fabrication method was developed to build the functional parts of the valve. and A.E.O. As shown in Figure 5, an air compressor was used to supply compressed air (CDA) to a pressure controller (OB1 Base MkIII, Elveflow, Paris, France). Careers.

This article is an open access article distributed under the terms and conditions of the Creative Commons Attribution (CC BY) license (, microfluidic, passive valve, ultra-low pressure, flow control, high flow rate.
prefill hydraulic 1/4 and 1/2 sizes in PVC, Natural Polypro, PTFE or PVDF. Harper J.C., Andrews J.M., Ben C., Hunt A.C., Murton J.K., Carson B.D., Bachand G.D., Lovchik J.A., Arndt W.D., Finley M.R., et al. Finally, the cover, the bonded seal layer, and the membrane, and the bottom were assembled together layer by layer through the orientation pillars and holes (Figure 4c). Anjewierden D., Liddiard G.A., Gale B.K. {{#pushedProductsPlacement4.length}} (g) Image showing the ellipsoid surface of the bottom at position B in Figure 4d. ; validation, A.E.O. The explosion view shows the four parts of the valve, and the cross-section view shows the inner structure of the valve. In comparison with the previously reported passive valves, the valve proposed in this work achieved a higher flow rate at a much lower threshold pressure, as shown in Table 1. The microvalve was demonstrated to successfully regulate the steady flow delivery in the system under the low driving pressures produced by the above gas sources. Due to the five-layer stacked architecture, the valve achieved a high flow rate of 2.79 mL/min with a low threshold pressure of 10 kPa. Bring us your difficult projects. The ellipsoidal surface design of the control chamber leaves quite an accommodating enclosure for the membrane to deflect into, thus facilitating a flow resistance development that could increase significantly, even under the low pressures. (973) 256.3000 Fax (973) 256.4745, California Warehouse: 2019M651643), Jiangsu Planned Projects for Postdoctoral Research Funds (No. Used in applications where back flow is not permitted, or must be redirected. 2019K033), and the Changzhou Sci and Tech Program (No. To learn more about Specialty Manufacturing Company's other product and service options visit these websites: Value added engineering-custom capabilities and 100 years of know how.
Sitemap 11