And because of this, it is a lengthy topic of engineering science to go through. I will however, briefly describe the difference between the two to aid your understanding in the generation of engineering technical drawings, imagine we assign a view a as the primary view. And we also then want to reduce this down to just a single decimal place. And then I'll just increase the font size, gets a little bit more space to be, to use us. Okay, so we've got a fully dimension drawing. So there is the video solution to project 5.1. Perhaps I can put it in there and then bring this 72 out a bit more. Flattened is where all components in the assembly will be detailed in the bomb without showing a relationship of components to subassemblies. We've also got another shortcut which is quite useful. 575 actually has a tolerance band of 0.05. Obviously, 360 degrees corresponds to a complete revolution. This middle section is bland and has no real features. Always carry out a check when you export to see if all the pages on your drawing of there, but also everything that you intend to have displayed on my drawing is that too. You need to ensure you keep to a character limit. However, my experience over the last ten years or so in technical drawing creation would mean that it is essential for me to do as it dramatically improves the clarity. We have a site button on the right, which gives a fantastic amount of control over often neglected, but in my opinion, important options as well as some general use parameters. So it's 20. Using the symmetrical method that would look like this, using the deviation method, using the limits method, and then using the basic method, it would look like this. Insert a row below, insert a column to the left of the cell or to the right. At this point you can adjust properties like Scale and Reference in the Sheet properties dialog. Then drag the balloon to one of the lines and place the balloon down. Regarding the screenshot programs I will try them tomorrow. Finally, the virtual sharp tool is helpful in obscure cases to articulate what it does. Ask questions and join in the discussions about everything Onshape. I can change the precision with this drop-down menu to see that are typed number remains and it is just displayed as a rounded number. In the first angle projection view convention, the view from the right view see is placed on the left side of the main view. There are a number of parameters to welding, including specific processes, shape, and quality of weld. Which file format you save as is dependent on what you'll be using the drawing print for. And then I'm going to delete this line and this line and then add in my title, which I'm just going to call exercise 5.1 B. And I'm also because of the bearing requirements, I need to put it in a max as well. The first tool allows us to add a center line by picking two midpoints. Let's select the dimension tool. I try and make sure that none of the components overlap. The finish of the component. Then from the New menu that appears, we can select Create, Drawing. Then select the view we want to create a whole table from the menu altars and the origin boxes highlighted. Engineering technical drawings should have borders of 10 millimeters from the trimmed edge of a sheet, except on the left-hand edge of a sheet. As the A3 printers are common in most companies. If we were to click on these folders, you will probably find nothing is populated in this pain. Leader lines are extremely helpful in technical drawings. 3. Would you like to become a designer and create your own products but dont know where to start? We've got some new site buttons, like in part design, which are hidden pains full of useful tools and settings. So now add some dimensions in. These two points are diagonally opposed, which represent the bounding box for your picture. So lastly, this section view down here. And then I'll put em 60 thread to 16.5 millimeters. And then we navigate to the relevant 3D model. So click there. Inserting Geometric Tolerances: Geometric tolerancing is an important part of 2D engineering technical drawings. The teacher's recommendation is shown until at least 5 student responses are collected. So I can select this view and then select broken out section view. We can also make the surface finish applied to all surfaces of the component by selecting this option here.

And your detail views from zed going the reverse direction through the alphabet. As I get a local copy of the file and opens the drawing and a new tab in the web browser. We have more than one break bobbin. So this will be diameter of 0.1. This box B is used if you want to specify an additional surface finish requirement, also given as a number in microns like our z, which is the difference between the tallest peak and the lowest valley in a service finished trace. Welcome to the Onshape forum! You can start off with the selection and C or ISO. Why not put one in for this hole here? So yes, so on this diameter and the stomata. So I'm going to start off with putting in some dimensions for this top-left view. My preference is to use the limit method. Is someone using a join since they cannot see some of the pages, the sheets option would be the first thing I check. If something can be misinterpreted on a drawing, it's wrong. ?L>S,pTey1bF5 +un8U|b!#ZPtFh#|>RZa|g'PmxT65[XX xdbf0Y,[irk,\t[ksRT!pJ"3#qME1H[PcOqNo6#Wn^_N%TH~WHCval
@`Z2d&m
Be bb9K%TFH6!4jZ]jU>&]:{kNHiJhlK:MWI%dG)e Then we can delete our lines. If you select one view by left clicking once and selecting the mouse button on a second view, and then dragging those views around the page. So I should put in dimension over here. So you'll have to create this using the note tool. All the way through. And this precision should be one decimal place. And then the depth of cut, we can say is up to entity. Foreshadowing a tool that we'll be looking at in a lot more detail later on. If I reference any mouse controls in the future, it will be based around the SolidWorks variant. But as you have set a cut line and Direction, section views can be aligned independently of their cut line. We can add various columns to our default bomb table by clicking on this drop-down menu and selecting as desired. For example, we can click here, here and here, which gives us a pitch circle diameter that aligns with the bright disk mounting flange and the center of the wheel bolt holes. Manipulating these blue circles will move the center point location. A good thing to check. Okay, so now let's talk about view representation. When we confirm this change, you can see that the letter below the digital view change to, as did the Detail View. As some manufacturing processes can work directly from 3D CAD models or directly read a 2D profile in. So do the same with the 60. I want to section this view up to the center line of the ball. After machining operations have been performed. So I'm just going to add a bit of text in here placeholder. Surface design, which uses points, lines, and surfaces to create models, is still used when feature-based modelling doesn't allow creation of certain components. So we'll click on the front hub part model. And on the views tab, we have the projection angle. This sets your font, font size, bold, italics, and color. Size is a field linked to the Title block and can be selected from the Fields dropdown in the Notes panel. Potentially a more warring problem with this method though, is that you can mess with the projection convention. Note our extension lines do not quite touch our geometry. And you have coach a visualization, which is not really something that I use, but it is something that has been used by people in the past. And in the next video, I'll take you through a worked example of how you can recreate this drawing. And this one as well, I'm gonna put here there's a there's a reason for that. But it will be best practice to write this in lowercase. These are models which we've created in the 3D modelling section. This could also have been in shop step or an internal radius. Completing the Title Block: When we load up an odd shaped template, standard or customized, you may notice some gray boxes with text in the title block. And then I'll put a new line on a 100 millimeter pitch, pitch circle down to. Onshape drawing templates contain multiple sheets: the main sheet and continuation sheets. This appears to be a clean and clear way of representing this part, sticking with the philosophy or showing all the details with as few views as possible. I'd like to have a bit more space between here.
onshape And we can also snap a dimension along the midpoint of its dimension line. And then I'm just going to center that to make it look a bit neater. Selecting portions of the text and then changing the font will allow us to do this. So that will be helpful for some of the dimensions that we need to add in. For example, if you'd let the supplier to laser mock, vibe, rewatch, or scribe identification marks. You will have a machinists or manufacturing engineers looking at your drawing to work out what cuts the need to make to make a work piece. This sheets, however, is missing some important details that you'd want to see on an assembly drawing. So it looks nice. Inserting a Standard View: Let's start putting some views into our drawings. You can make any changes to the new sheet you wish, without affecting the original sheet. We'll have a look at the upright suspension component. You can merge the cells too. It looks like you're new here. Inserting Notes and Callouts: Our 2D engineering technical drawings will often need various kinds of notes and annotations. For sheets with parts involved in a release process, the part number and state are displayed next to the part name, as shown above, Detail and Section views are shown with their view identifiers, as shown above. You can do this by writing in the notes or by putting in a standalone notes somewhere your title block, or even put it in the title block stating a general service finish of RA 3.2 microns, for example, for machine components. So what we can then do is we can copy that because we were, we'd need to use that again. Think. These will be multiple sheets within one drawing. In this application. You can also duplicate an existing sheet and use that as a template to make small changes, such as changing the configuration of a part or assembly. Whereas this drawing doesn't appear to be quite right to me, as it feels a bit messy. I copied a sketch but i would like to scale down in size. For example, this means when a unit is divided by a 1000. You need to select the location of the cut line. So not that. This button simply toggles between whether an AAC is dimensioned as a radius or a diameter. So undo that as 100.
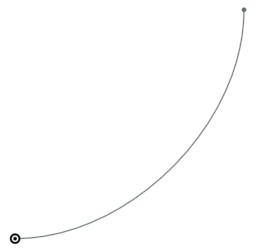
So I think actually I might put in a projection view over here. The first handles the templates that you may have created or those that aren't shape has created as part two different international standards. And we also want to chamfer the first thread. We can demonstrate this tool using a simple component like this with multiple holes. Just needs to then click the Get Started and fill in a few more details. Many people do not like this and right, do not scale on the drawing, which is banning what I just described. For the tab that you have selected. An auxiliary view usually only contains a small feature which I need to dimension. (All names of parts, Part Studios, and Assemblies used in views on the sheet are listed here.) In most scenarios, no point 35 and no 0.7 millimeter line weights are suitable for most applications, but for manual and CAD drawings. 25. And then we just need to fill out the details. But this time we will select exploded view rather than isometric front or the rest of the normal views. Then I can do another one down here. And I suggest that we use just for rows and one column.
We can take one of these templates and modify them. Let me, let me go delete and delete. Some of these may not be worth it, but it's probably based on user preference. 22. And we have these symbols to if you right mouse button click on the note. So this tolerance is actually one. We can tidy our detail view label further by adding a prefix such as Detail View. For example, this represents view a from the previous shape that you looked at, VB and VC and so on. So I can put in some more, sorry, this one to here. To access the properties of a drawing, right-click on the Drawing tab and select Properties. And then I'm going to put in exercise 5.1 C. And once again, I'm going to increase the font size two. Here.
catia v5 videotutorial walden For these latter manufacturing processes. 3d CAD models should always be modeled as one-to-one scale. And this indicator changes in line with the name of the sheet. Well, sorry, we don't need to scale level because it is one-to-one scale. Pressing the Escape key then allows you to grab these blue circles and drag them into different positions in order to modify the spline shape On Shape now needs to know to what depth you want to cut too.
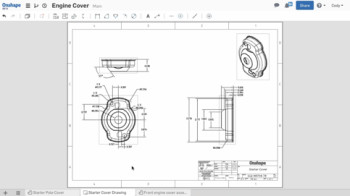
So just put in hopes I'll put in the lower box. These comments might reference notes on a variant EEG color or finish. We can make these center lines in an alternative way by using our second tool. Our tolerance band for our surface is plus or minus 6.5 microns, which is naught point naught, naught 65 millimeters. I placed another dimension and scaled it a second time, Meaning I didnt even have to draw a line, Then, I decided to change the scale of that imported dxf I changed that distance from 7 to 5, And Alexander, I agree with you. So let's have a look at those. In contrast, for this bearing diameter, we may want to increase the precision and go to three decimal places. The line does not change to the brown color that we normally see when we select a point or a line.
Sitemap 31