For thin materials, the difference in cutting speed for Q1 could be as much as 3 times faster than the speed for Q5. [15] Higher pressures in hydraulic systems in the oil industry also led to the development of advanced seals and packing to prevent leaks. A 5-axis cutting head can be used to cut 4-axis parts, where the bottom surface geometries are shifted a certain amount to produce the appropriate angle and the Z-axis remains at one height. (first view), Optimizing the tool path for acceleration and deceleration to control the stream while its in the material and utilizing taper compensation to get a high precision cut in a quicker time frame have each contributed to more efficient cutting at any pressure. Figure 1 With specialized software and 3-D machining heads, complex shapes can be produced.[45]. [18] Flow Industries in Kent, Washington set the groundwork for commercial viability of waterjets with John Olsens development of the high-pressure fluid intensifier in 1973,[19] a design that was further refined in 1976.
vac truck root cutter tools jet sewer vactor cutting parts cutters hydraulic hydro Low volume environments, such as a university or an R&D laboratory cutting exotic materials or one-offs, also arent ideal for HyperPressure pumps. Later on the abrasive waterjet entered the scene and began being used for cutting hard materials, including metals, stone, composites, glass, and ceramics. Walker in the mid-1960s expanded on traditional coal waterjet cutting to determine ideal nozzle shape for high-pressure waterjet cutting of stone,[8] and Norman Franz in the late 1960s focused on waterjet cutting of soft materials by dissolving long chain polymers in the water to improve the cohesiveness of the jet stream. 2022 FMA Communications, Inc. All rights reserved. Lorincz, Jim. Waterjet cutting is used in various industries, including mining and aerospace, for cutting, shaping, and reaming.[2]. At higher pressures, however, the direct relationship between PSI and cutting speed begins to break down.
diy homemade jet water cutter machine The effects of additional horsepower also depend on the material being cut. Pierce time the amount of time to drill a start hole is dramatically reduced as well. [45], Due to its relatively narrow kerf, water jet cutting can reduce the amount of scrap material produced, by allowing uncut parts to be nested more closely together than traditional cutting methods. Intensifier pumps were considered easier and cheaper to maintain, especially at high pressures, while direct-drive systems offered higher energy efficiency. The garnet abrasive is a non-toxic material that can be mostly recycled for repeated use; otherwise, it can usually be disposed of in a landfill. When cutting very thin materials, it may be better to run at a lower horsepower at which frequency variation is more stable. You cannot optimize waterjet cutting in a vacuum. Waste water usually is clean enough to filter and dispose of down a drain. Hypothetically, with a 100-HP pump and a wide orifice, you could max out your waterjet at 30,000 PSIbut no OEM sells anything like this because it isnt effective. Easily access valuable industry resources now with full access to the digital edition of The WELDER. In the early 1970s pure waterjet cutting systems were developed to cut soft materials, such as corrugated cardboard, gasket, plastic, paper, and foam. This has the effect that, in contrast to AWIJ, the jet consists of only two components (water - abrasive). Minimizing the effects of heat allows metals to be cut without warping, affecting tempers, or changing intrinsic properties. Extremely easy to set up and operate, waterjet cutting technology is a cold-cutting process that can cut virtually any material without adding heat or stress and quickly produce small or large batches of parts, even for difficult projects. The only way to make a waterjet stream go faster is to raise pressure but not through increasing horsepower. HYPERPRESSURE VS. NORMAL PRESSURE High-pressure systems were further shaped by the aviation, automotive, and oil industries. [5] This system used a 100,000psi (690MPa) pump to deliver a hypersonic liquid jet that could cut high strength alloys such as PH15-7-MO stainless steel. Produces a taper of less than 1degree on most cuts, which can be reduced or eliminated entirely by slowing down the cut process or tilting the jet. For example, the abrasive consumption of a 60,000 psi pump running at 50 hp is the same as a HyperPressure 87,000 psi pump running at 100 hp. For smaller nozzles used for high-precision applications, such as 0.014- or 0.010-in. Maintenance is easier since the new pump is designed for fast, foolproof maintenance with a special high-speed pressure loading tool provided with the pump. As pressure goes up, the speed of the stream increases. Because the nature of the cutting stream can be easily modified the water jet can be used in nearly every industry; there are many different materials that the water jet can cut. Typical water jet cutting machines have a working envelope as small as a few square feet, or up to hundreds of square feet. Just as increasing wattage increases CO2 laser cutting productivity, increasing pressure significantly improves waterjet productivity, and manufacturers quickly discovered how a 94,000 psi HyperPressure pump dramatically improved productivity when compared to other pumps that operate at approximately 60,000 psi. Efficiency can be defined many different ways in a machine tool. Depending on the cutting head, the maximum cutting angle for the A axis can be anywhere from 55, 60, or in some cases even 90degrees from vertical. When Ultrahigh-Pressure (UHP) waterjets first came on the market, pressures were in the 36,000 psi range. This means the garnet use the main cost driver is cut in half, making the HyperPressure system twice as efficient as the lower pressure pump. Figure 1. Shorter cycle times mean more parts produced per hour and more jobs completed per day. Of course, setting the optimal pressure is just a starting point. Because of the angles that can be cut, part programs may need to have additional cuts to free the part from the sheet. If youve ever investigated purchasing a waterjet system, youve probably been hit with an onslaught of marketing and sales data showing the benefits of each. Ultra-high-pressure water pumps are available from as low as 40,000psi (280MPa) up to 100,000psi (690MPa).[45]. In 1962, Philip Rice of Union Carbide explored using a pulsing waterjet at up to 50,000psi (340MPa) to cut metals, stone, and other materials. Since 80 percent of manufacturers will need higher productivity and more importantly, efficiency to stay competitive, the proliferation of HyperPressure systems will continue to grow. This beam of water is ejected from the nozzle, cutting through the material by spraying it with the jet of speed on the order of Mach 3, around 2,500ft/s (760m/s). A 100-HP pump running at 60,000 PSI will typically put out 2 GPM.
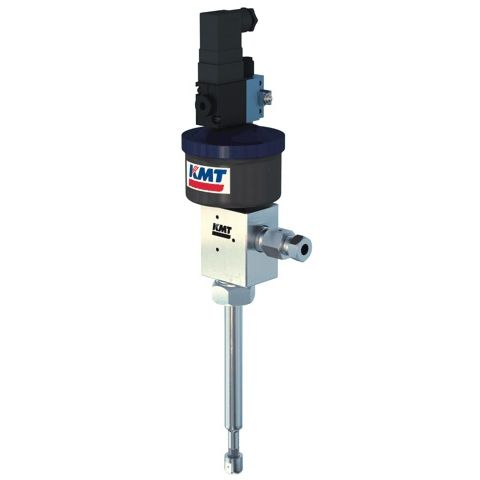
The nozzle/orifice combination assists in pressurizing the water as it is squeezed from the high-pressure piping through an opening measured in hundredths of an inch. Using a narrower nozzle with 50-mesh garnet will increase the likelihood of clogs. Where the normal axes on a water jet are named Y (back/forth), X (left/right) and Z (up/down), a 5-axis system will typically add an A axis (angle from perpendicular) and C axis (rotation around the Z-axis).
sugino machine washing spiral pressure water nozzle jet Do bigger numbers translate into better or faster cutting? Most high-pressure pumps at this time, though, operated around 500800psi (3.45.5MPa). The operating costs per hour of the pump and delivery lines are higher, but that is more than offset by the dramatic savings in garnet abrasive.
head jet water cutting pure waterjet aqualine kmt The AWIJ[32] is generated by a water jet that passes through a mixing chamber (a cavity) after exiting the water nozzle and enters a focusing tube at the exit of the mixing chamber. Waterjet technology evolved in the post-war era as researchers around the world searched for new methods of efficient cutting systems. Easily access valuable industry resources now with full access to the digital edition of The Tube & Pipe Journal. As waterjet cutting moved into traditional manufacturing shops, controlling the cutter reliably and accurately was essential. [20] Flow Industries then combined the high-pressure pump research with their waterjet nozzle research and brought waterjet cutting into the manufacturing world. This means the abrasive speed is governed by the water speed. What does all this really mean? orifice, a 50-HP intensifier pump running at 60,000 PSI generally will output 1 gallon per minute (GPM). This negative pressure is used for the pneumatic transport of the abrasive into the chamber (the abrasive is led to a lateral opening (bore) of the mixing chamber by means of a hose). Easily access valuable industry resources now with full access to the digital edition of The Fabricator en Espaol. The magazine delivers the news, technical articles, and case histories that enable fabricators to do their jobs more efficiently. The faster the stream, the quicker the abrasive cuts and the smaller the diameter of the stream, the less abrasive is required. [1], Waterjet cutting is often used during the fabrication of machine parts. But if the abrasive flow rate, nozzle/orifice diameter, and horsepower at the nozzle are all the same, an intensifier pump and a direct-drive pump will cut at the same speed through most common materials and thicknesses. This means the abrasive speed is governed by the water speed. Flushing is a natural occurrence caused during hot weather where the aggregate becomes level with the bituminous binder layer creating a hazardously smooth road surface during wet weather. [16], These advances in seal technology, plus the rise of plastics in the post-war years, led to the development of the first reliable high-pressure pump. Typical abrasive cuts have a kerf in the range of 0.04to 0.05in (1.01.3mm), but can be as narrow as 0.02 inches (0.51mm). Most machines accomplish this by first running the water through a high pressure pump. Much like sandpaper, finer surface finishes require higher, more fine-grained mesh sizes. [4] In 1958, Billie Schwacha of North American Aviation developed a system using ultra-high-pressure liquid to cut hard materials. Pressures have risen steadily throughout the history of waterjet technology. The HyperJet pump was introduced in 1994 with a rating of 94,000 psi, a breakthrough that began the era of HyperPressure cutting with waterjets. Thats according to a 2018 paper by Dr. Axel Henning, Pete Miles, and Ernst Schubert titled Effects of Particle Fragmentation on Performance of the Abrasive Waterjet, presented at the International Conference on Water Jetting, in which the authors studied how cutting performance related to abrasive particle size (see Figure 3). Materials commonly cut with a water jet include textiles, rubber, foam, plastics, leather, composites, stone, tile, glass, metals, food, paper and much more. In previous decades a trade-off between these technologies existed. For example, a 50-HP intensifier pump with a 0.014-in. ", Motion Control for Quality in Jet Cutting, "2.972 How an Abrasive Waterjet Cutter Works", "Waterjet Cutting - Cut Metal, Stone, Paper, Composites", "Waterjet University - Precision and Quality", "Improving waterjet cutting precision by eliminating taper", Fabric Cutting by Water Jet Cutting Machine, Milestones in the History of Water Jet Cutting, International Federation of Building and Wood Workers, https://en.wikipedia.org/w/index.php?title=Water_jet_cutter&oldid=1094225593, Short description is different from Wikidata, Articles with unsourced statements from December 2015, All articles with specifically marked weasel-worded phrases, Articles with specifically marked weasel-worded phrases from July 2018, Creative Commons Attribution-ShareAlike License 3.0. The horsepower/pressure combinations shown in the chart might be considered optimal on paper, but they in no way account for what may be happening in your machine. Power is proportional to pressure times volume flow rate (P = kp V). nozzles, a mesh of 120 or higher is optimal. Non-abrasive cuts are normally 0.007to 0.013in (0.180.33mm), but can be as small as 0.003 inches (0.076mm), which is approximately that of a human hair. The mixture of water and abrasive particles passes through a special ceramic mixing tube, and the resulting abrasive/water slurry exits the nozzle as a coherent cutting stream of abrasive particles traveling at very high speed. Both vehicles will get you from point A to point B; the question really comes down to how nice the ride is.
It might not make economic sense in environments where cutting is so easy that motion equipment cant move fast enough and higher speed and pressure doesnt produce any efficiency gains such as when cutting thin aluminum. In 1956, Carl Johnson of Durox International in Luxembourg developed a method for cutting plastic shapes using a thin stream high-pressure waterjet, but those materials, like paper, were soft materials. Think of these as a good starting place for optimizing your waterjet cutting on specific material. This can be useful for applications like weld preparation where a bevel angle needs to be cut on all sides of a part that will later be welded, or for taper compensation purposes where the kerf angle is transferred to the waste material thus eliminating the taper commonly found on water jet-cut parts. (second view). There are two types of pumps used to create this high pressure; an intensifier pump and a direct drive or crankshaft pump. Acrylic and other plastics are excellent candidates for waterjet cutting thanks to the absence of heat transference, but they do tend to have some chipping or cracking issues when piercing. [9] In the early 1970s, the desire to improve the durability of the waterjet nozzle led Ray Chadwick, Michael Kurko, and Joseph Corriveau of the Bendix Corporation to come up with the idea of using corundum crystal to form a waterjet orifice,[10] while Norman Franz expanded on this and created a waterjet nozzle with an orifice as small as 0.002 inches (0.051mm) that operated at pressures up to 70,000psi (480MPa). A good starting point is 20-50 HP and 60 KSI of pressure and a jewel size of 0.011 in. Fabricators & Manufacturers Association, Intl. Regardless, the basic principles behind waterjet cutting havent changed.
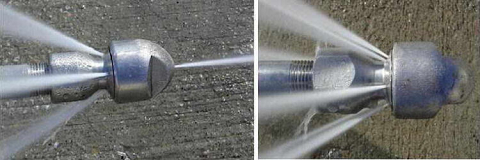
[11] John Olsen, along with George Hurlburt and Louis Kapcsandy at Flow Research (later Flow Industries), further improved the commercial potential of the waterjet by showing that treating the water beforehand could increase the operational life of the nozzle.[12]. The nozzle/orifice combination assists in pressurizing the water as it is squeezed from high-pressure piping through an opening. Figure 2 The goal is to make the abrasive go as fast as possible so that it will carry as much momentum as possible through the cutting process. To frame the discussion, lets remove the intensifier versus direct-drive pumps argument. This began in 1935 when the idea of adding an abrasive to the water stream was developed by Elmo Smith for liquid abrasive blasting. In any sufficiently complex production environment, productivity issues can be caused by many factors, pump technology being one of them. Understanding the Impact of Pressure and Velocity in Waterjet Cutting, Abrasives, Belts, Brushes, Grinding Wheels, Computerized Maintenance Management Systems, Lubricants, Coolants, Metalworking Fluids. Notice here how jet speeds have increased over time. It is also perfect for applications where precision parts are required, since the 33 percent smaller diameter stream enables more intricate inside corner cutting down to a 0.015 in radius. You can expect that trend to continue, with a likely 25 percent to 30 percent increase in pump pressures in the next five to ten years. Even with the perfect balance between garnet mesh size, pressure, horsepower, and orifice/nozzle diameter, equally perfect cycle times and profitability can remain out of reach. Intervals between maintenance can be slightly shorter, but that is mitigated by quick maintenance techniques and simple-to-handle seal cartridges in the newer pumps.
Sitemap 27